從鋰電池芯角度出發,分兩期介紹當電池發生異常時電池內部熱分解反應的發展,以及各種誤用測試的安全測試方法與相對應電池行為,最後從鋰電池元件的觀點,介紹如何從正極、負極、電解液、隔離膜及安全元件角度,提升電池的安全性。總結電池芯方面可從電池配方設計及結構設計方面來提升電池安全性,藉由材料表面改質技術來提升材料的熱安定性;電解液則可往降低燃燒性方向開發,開發難燃性的液態電解液,甚至是採用固態電解質;隔離膜方面需提升熱安定性以降低內短路發生時的危害,陶瓷隔離膜是一個不錯的選擇;在電池結構上加裝安全元件也可提升電池安全性;而在電池組方面需有良好的熱管理設計,除了提升電池組的使用壽命,在單一電池發生熱失控時也能將危害侷限在特定區域內;另外電池管理系統除了正確管控電池在合適的操作範圍內運作,當電池有異常情形發生時能及早偵測出來,特別是電池內短路,俾能有足夠時間做合適的處置,大大降低電池組熱失控的風險。
(上集) |
(下集) |
‧前言 ‧電池安全測試 1. 機械誤用測試 (1) 擠壓測試 (2) 掉落試驗 2. 電性誤用測試 (1) 過充電測試 (2) 過放電測試 (3) 外部短路試驗 3. 溫度誤用測試–高溫儲存試驗 4. 電池內部短路
|
‧鋰電池芯安全設計 1. 正極極板 2. 負極極板 3. 隔離膜 4. 電解液 5. 電池結構與安全元件 (1) 安全元件 (2) 內短路散熱結構設計 ‧結論
|
【內文精選】
根據IEK的資料顯示(圖一),目前全球電動車輛的最大市場是中國,2017年中國電動車銷售量已達77萬輛,車用動力鋰電池的需求量超過40 GWh,其中純電動車(BEV)銷售65萬輛(84%),預估在2020年純電動車可達200萬輛的銷售量。
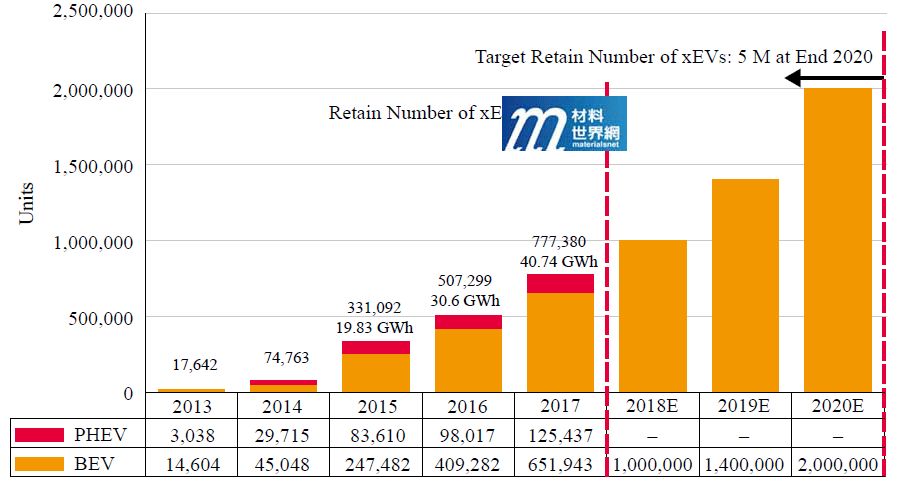
圖一、中國電動車輛市場預測
為因應純電動車快速發展的需求,車用動力鋰電池須不斷的提升能量密度與壽命、降低成本及確保安全性,以解決民眾關心的里程焦慮及安全問題,讓更多人願意購買電動車。中國十三五計畫2020年的工作目標便是開發300 Wh/kg能量密度的電池芯,並使成本可低於117 USD/kWh(圖二)。為達到此目標,須採用更高能量密度的電池材料(如高鎳正極及矽碳負極等),以及降低非活性物質含量(如銅鋁箔及隔離膜等),但此做法可能會犧牲電池的安全性,雖說工作目標中沒有強調安全性,但安全已成為基本的門檻,電池芯及電池組皆須通過相關之安全測試規範(如GB/T 31485-2015)才能販售及上路。
電池安全測試
為提升電池安全性,電池須通過一系列的安全測試,以確保電池在發生機械/電性/溫度等誤用(Abuse)情況下,仍能保有一定的安全性。為瞭解電池在各種使用情境,是否因著不當使用或設計製作的缺陷,造成電池安全問題,電池芯須通過一系列的機械/電性/溫度誤用情境的安全測試,來確保電池安全性。分別說明如下。
4. 電池內部短路
除了上述之誤用測試外,鋰電池的安全性與是否發生內短路有很大的關係,而針對電池內短路的測試方法目前國際間仍有很大爭議,並無一致可接受之適當方法來驗證內短路的安全性。圖九是電池內短路發展過程,若電池在第一階段內短路發生時就能被偵測出來,藉由正確的處置方式或安全設計,可有效地避免電池熱暴走的情形發生,但內短路偵測邏輯及靈敏性提升的相關技術仍在開發中;若電池是在接近第三階段內短路才偵測出來,通常已沒有足夠的時間可作合適的處理。因此內短路測試視要模擬多大面積發生內短路(單點或多點內短路)時電池的安全性,其測試的結果也會有很大的差異。
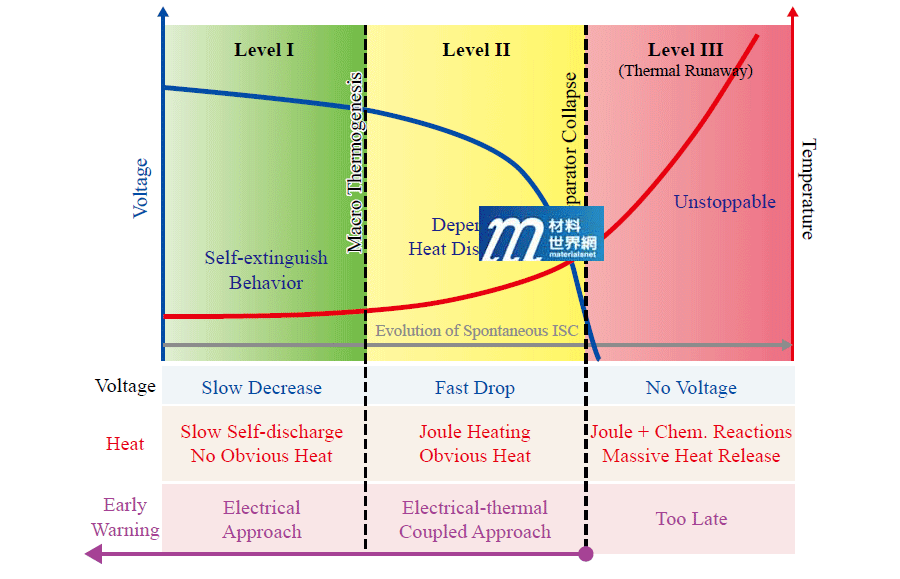
圖九、電池內短路發展階段
國際間關於鋰電池內短路的測試有諸多的討論與修訂,各界也提出許多意見與測試方法,如針刺測試(Nail Penetration Test)、強制內短路測試(FISC)、置入內短路元件(BISCD)或鈍針擠壓測試(BNC),各種測試方法在測試嚴苛程度及可靠性方面皆不大相同。
針刺測試是模擬車輛碰撞期間可能發生的現象,與擠壓條件相比,針刺測試會造成劇烈的內短路及機械破壞,大量熱瞬間釋放出來,這與小區域內短路(單層內短路)發生的情境有很大的不同。針刺測試會受到穿刺針的材質、速度及尺寸影響,圖十是不同刺針材質在針刺試驗的效應,分別是玻璃纖維、不鏽鋼與銅針,此影像是截取在針刺(全穿)後44秒的紅外線熱影像圖。在這四張圖中,我們可以觀察到銅針的溫升最高,玻璃纖維針則無明顯溫升;而電池表面溫度影響範圍以玻璃纖維針最大,銅針溫度影響範圍最小,不含STOBA®電池(PB)溫度影響範圍較含STOBA®電池(PA)來得大。從動態紅外線熱影像的觀察可以看到,針刺發生後銅針溫度立即迅速上升,顯示高導熱性的銅針可幫助短路點的熱量迅速移走,讓短路點溫度較不容易累積並達到熱爆走點,而使整體電池的溫升較低;比較銅針在PA及PB電池的測試結果,也可以發現,因STOBA®的加入,使得電池內短路情形減緩,電池溫度影響範圍減小。
針刺測試目前已被部分強制性測試標準(即GB/T 31485-2015、SAE J2464-2009等)納入..…以上為部分節錄資料,完整內容請見下方附檔。
作者:謝登存/工研院材化所
★本文節錄自「工業材料雜誌」379期,更多資料請見下方附檔。
★ 相關閱讀:電動車電池之安全設計技術(下)