從鋰電池芯角度出發,分兩期介紹當電池發生異常時電池內部熱分解反應的發展,以及各種誤用測試的安全測試方法與相對應電池行為,最後從鋰電池元件的觀點,介紹如何從正極、負極、電解液、隔離膜及安全元件角度,提升電池的安全性。
(上集) |
(下集) |
‧前言 ‧電池安全測試 1. 機械誤用測試 (1) 擠壓測試 (2) 掉落試驗 2. 電性誤用測試 (1) 過充電測試 (2) 過放電測試 (3) 外部短路試驗 3. 溫度誤用測試–高溫儲存試驗 4. 電池內部短路
|
‧鋰電池芯安全設計 1. 正極極板 2. 負極極板 3. 隔離膜 4. 電解液 5. 電池結構與安全元件 (1) 安全元件 (2) 內短路散熱結構設計 ‧結論
|
【內文精選】
鋰電池芯安全設計
了解鋰電池的異常行為及相關的安全測試之後,接著從鋰電池芯的組成元件觀點,探討從正極、負極、隔離膜、電解液、罐體結構及安全裝置,如何可增加電池的安全性。
1. 正極極板
鋰電池電容量的提升與電池所採用的活性物質有關,其中又以正極材料最具關鍵;正極用量在電池中比重最大,正極材料分解反應的放熱量也占主要部分,因此正極材料對整體電池安全性的影響也相當大。
為解決高能量正極所引發的安全問題,可在正極材料進行表面改質,防止正極和電解液直接接觸,從而抑制相變,提高結構穩定性。表面塗層材料需具有耐熱熱和化學惰性,通常是磷酸鹽、氟化物和固體氧化物等,如AlPO4、AlF3、ZrO2。也可在極板中加入特殊的安全材料,如工研院開發的STOBA®,使電池能通過嚴苛的針刺試驗。
4. 電解液
電解液中主要是由鋰鹽、有機溶劑及機能性添加劑所組成,需滿足高導電度、穩定電化學特性、低成本及安全等特點。電解液的配方除了對電池電性有很大的影響外,對電池安全性的提升也有很大的貢獻。在安全性方面,電解液中可加入添加劑來提升電池防過充、阻燃或其他功能性。在過充添加劑方面,CHB (Cyclohexyl Benzene)及BP (Biphenyl)是常見的聚合型防過充添加劑,氧化還原對(Redox Shuttle)則是消耗過充電量的添加劑。
電解液中的有機溶劑可燃性高,若電解液燃燒,釋放的熱量會高於其他材料熱分解熱量的總和,因此阻燃電解液是電池廠追求的目標之一。為達到良好的阻燃效果,通常需加入較大量的添加劑,因此影響到電池正常的電性表現。圖十六為TBBP電解液添加劑的阻燃效果,藉著優化阻燃添加劑的含量(1%),可使電池循還壽命不受影響,也能保有良好的阻燃效果。一般電解液之電池經點火後立刻起火燃燒,並維持約12分鐘;若電解液中含1%之阻燃劑時,雖然電解液點火後仍被點著,但僅有小火點著,且僅維持17秒便自行熄滅,可大幅提升電池安全性;若加到3%添加量…以上為部分節錄資料,完整內容請見下方附檔。
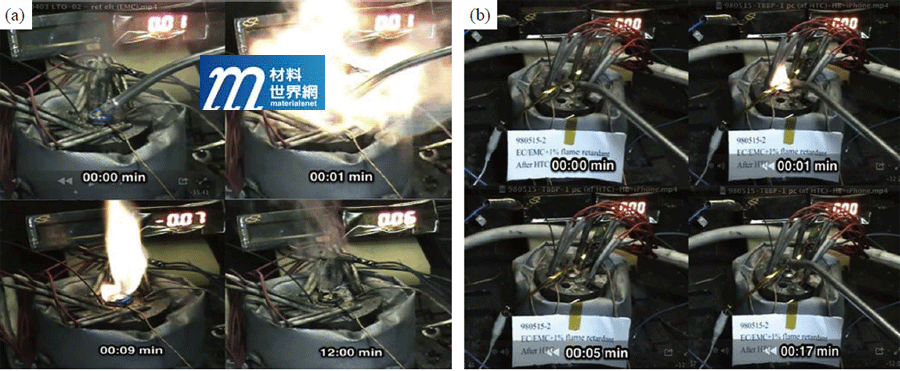
圖十六、18650電池燃燒測試(a)標準電解液;(b)含1% TBBP阻燃劑之電解液
5. 電池結構與安全元件
車用電池的設計依其外型可分為圓柱形、方形和軟包裝電池三種類型。軟包裝電池因扁平結構具有較佳的散熱途徑,可將電池內部產生的溫度較快速的傳導到外面,使電池相對較安全;但因先天結構的限制,電池殼體通常沒有引入安全元件的空間,僅可在電池外部連接通路上加入安全元件來提升電池安全性。圓柱形及方形電池是屬於硬罐體電池,罐體具有較佳的剛性及空間加入安全元件,來提升電池安全性。
(1) 安全元件
18650電池因其電容量小且有多道成熟的安全設計,相對於其他形式之電動車用電池有較佳的安全性。18650電池的安全元件多設計在端蓋組(圖十八)上,PTC (Positive Temperature Coefficient)元件在溫度升高時阻抗會上升,藉此限制異常大電流的流通來保護電池;CID (Current Interrupt Device)元件則可因電池內部壓力升高,使CID上下盤變形,造成連接點分離而截斷電流通道;而安全閥(Safety Valve)元件是當電池內部壓力過大時會破裂,釋放壓力使電池安全;鋁線連接(Al Wire Bond)用在電芯與模組間的連接,當有高電流異常情形發生時可像保險絲一樣被燒熔,來確保電池模組/系統安全,在Tesla電動車上被廣泛應用。
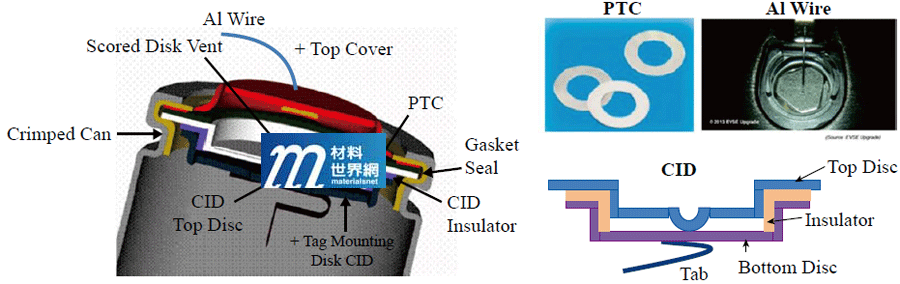
圖十八、18650電池安全結構(PTC/CID/Al Wire)
方形電池罐體結構的安全設計與18650電池不同,安全洩壓閥是通用的安全元件之一,可在電池壓力上升時打開,以降低內部壓力;PTC元件則因通過電流較大…以上為部分節錄資料,完整內容請見下方附檔。
作者:謝登存/工研院材化所
★本文節錄自「工業材料雜誌」381期,更多資料請見下方附檔。
★ 相關閱讀:電動車電池之安全設計技術(上)