高功率模組封裝系統層級散熱設計
直接液冷的散熱方式是將DBC基板直接焊接於具有散熱器的底板上,不須外加界面材料,如圖十二所示,因此散熱性能顯著提升。由於模組結構和傳統模組類似,因此不會增加模組封裝製程困難度,而由於減少熱界面材料,因此熱阻較低,散熱效能增加。散熱器的散熱增強設計也可以有更多的方式,例如底板直接設計針狀鰭片,如此在系統設計時不須設計流道,只要挖槽使工作流體能通過鰭片將熱帶走,使得系統散熱設計較容易,也能讓功率模組維持較高的散熱效果。
微流道直接液冷的設計則是結合散熱器和DBC基板而不需銅底板的設計,如圖十五所示。散熱器製作須與DBC製程結合,實際設計可將兩個DBC基板和中間由多層銅層製作的微流道結構結合,另一種則是將DBC基板和銅層製作的微流道接合,如圖十六所示。銅層一般超過8~10層,流道由每層銅層的多邊形結構接合而成。由於可將微流道尺寸進一步縮小以增加散熱性能,缺點是結構較弱,可靠度問題須特別注意。
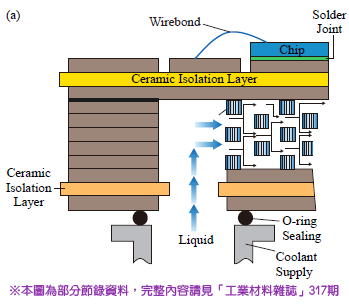
圖十六、兩種不同整合DBC的直接液冷微流道散熱設計
傳統間接液冷、微流道直接液冷及直接整合DBC微流道的散熱效果如圖十七所示。底板微流道直接液冷之散熱效果較傳統間接液冷散熱方式高,約降低60%的熱阻。而整合DBC微流道的散熱效果最好,較底板微流道直接液冷約可降低60%。尤其是使用熱傳導率高的氮化鋁基板,會有最佳的散熱效果。
由於功率模組一般採用單面散熱路徑的方式進行散熱,因此散熱增強設計往往會造成模組體積增加。另一種散熱增強方式是採用雙面散熱,在晶片上方貼附散熱結構,增加散熱路徑,以提升散熱效能,如圖廿所示。圖廿一為目前Lexus LS 600h車中的雙面液冷模組結構實際設計應用例,由於晶片產生的熱可由晶片兩面進行散熱,因此散熱性能較單面散熱佳,且可縮小體積。由於晶片上方有Emitter及Gate的電極,因此一般會以覆晶(Flip Chip)的方式進行連接,但各廠商的晶片結構設計有所差異,因此實際設計時,由於須考慮晶片上方的電性連接方式,設計較為困難。更重要的是,由於功率元件表面的金屬是鋁,無法和DBC的銅直接接合,一般會將元件在晶圓狀態下利用封裝前段製程加上其他金屬,以便於覆晶製程。
由於功率元件晶片具高電壓、高電流的特性,除了上下兩面導熱結構必須注意耐電壓電流的問題外,其間距設計及填充膠材料也必須注意。由於雙面液冷散熱設計和傳統模組散熱方式不同,因此在系統散熱須另外設計。圖廿二是TOYOTA的系統散熱設計,將雙面液冷的模組垂直插入系統散熱結構中,流體可由模組兩面通過,系統體積可大幅縮小。Alstom公司也設計雙面散熱的功率模組,利用金屬凸塊接合晶片上方,兩面基板下方以導線架形式將電源信號接出,並在導線架下方接合鰭片。系統應用時將兩組模組背面接合,並於兩面通過流體,利用此方式可縮小模組體積,降低模組重量……以上內容為重點摘錄,如欲詳全文請見原文
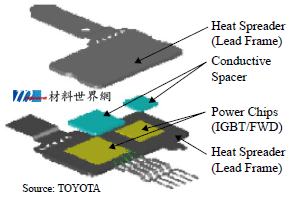
圖廿一、雙面液冷散熱功率模組結構圖
作者:劉君愷 / 工研院電光所