近年來,半導體 3D IC製程以及 3D封裝廣泛的被很多國際研究機構與廠商重視,而在 3D IC的技術中,矽導通孔(Through Silicon Via; TSV)、晶圓接合技術、晶圓薄化、薄晶圓的拿取是整個 3D IC中最核心的四大技術。其中TSV的形成應用了半導體後段銅製程技術,其餘三項則是為了製作 3D IC堆疊而發展。
以製作 TSV而言,它運用到的半導體製程技術包含:深離子蝕刻技術、次大氣壓化學氣相沉積、離子化物理氣相沉積、原子層沉積法、高深寬比填孔電鍍銅技術和化學機械平坦化。由於TSV為高深寬比的孔洞結構,不同於以往半導體的孔洞尺寸,本文將針對 TSV技術中的蝕刻方法、介電層、擴散阻擋層和銅晶種層鍍膜方法,以及電鍍方法以目前所用已接近量產之半導體製程技術作詳細介紹。
TSV製程流程簡介
矽導通孔的製程流程大致上與半導體後段製程雷同,首先利用黃光製程定義出圖形,接續使用深離子蝕刻技術(DRIE)蝕刻出 TSV的形狀,再利用次大氣壓化學氣相沉積(SA-CVD)沉積介電層,以及物理氣相沉積(IPVD)或是原子層沉積法(ALD)沉積阻障層與晶種層,並利用電鍍銅填充 TSV,最後再藉由化學機械平坦化(CMP)將所有的金屬層去除,詳細的製作流程,如圖一所示。
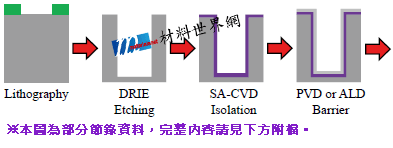
圖一、TSV標準製作流程
TSV介電薄膜沉積製程
目前量產型的 TSV介電薄膜材料以SiO2為主,依照不同的製程整合流程大致可分為兩種。①爐管式熱氧化製程以及②化學氣相沉積(CVD),其中 CVD為目前 TSV介電材料沉積量產的主力製程。由於TSV製程整合步驟不同,因此選用的沉積方法也有所不同。一般而言,電子元件的熱預算在 3D IC的製程階段約落在 400˚C以內,因此製程溫度在 180~400˚C之間的 CVD製程相較於爐管式熱氧化製程較為合適。CVD製程的氣體大致可分為 SiH4 和 TEOS 兩種。
TSV金屬薄膜沉積製程
在 TSV技術中,金屬薄膜沉積製程是指沉積擴散阻障層和晶種層。由於 TSV是高深寬比的孔洞,以目前的量產技術而言,離子化物理氣相沉積(IPVD)仍為主要方法。若 AR>15或 TSV開孔直徑<2 μm時,為了達到薄膜連續覆蓋的目標,原子層沉積法(ALD)是另一種選擇,但由於 ALD的設備成本過高,目前業界還是以 IPVD為主。
TSV填充製程
比較TSV電鍍製程與傳統積體電路內接線路的電鍍製程,最大的差異在於深寬比與線路大小,利用電鍍填充高深寬比的孔洞 TSV是一個難度高的技術,在這個製程中最關鍵的即是電鍍添加劑的配方比例。在 TSV填孔電鍍製程中,為了要達到孔洞填充目的,必須仰賴多種有機添加劑的配比方才可達成目的。
有機添加劑的種類一般可分為三種:①加速劑:目的在於加速銅電沉積的反應速率,由於沉積的銅薄膜有光亮的效果,因此一般 PCB工業稱其為光澤劑;②抑制劑:其目的在於利用質傳所產生出的濃度梯度,造成吸附在孔洞表面的抑制劑階梯覆蓋率的差異,達到不同孔口深度的電化學沉積速率差異,進一步達到填滿孔洞之目的……以上為部分節錄資料,完整內容請見下方附檔。
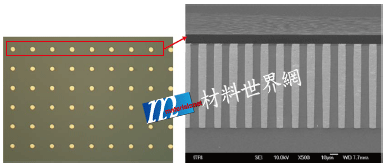
圖十六、5x50 μm TSV之CMP研磨後的SEM圖
作者:張佑祥、陳瑞琴、曾培哲/工研院電光所
★本文節錄自「工業材料雜誌」345期,更多資料請見下方附檔。