原子層沉積技術發展
原子層沉積技術最早稱為原子層磊晶( Atomic Layer Epitaxy; ALE ),是由芬蘭 Suntola 等人在 1974年開發出來,初期是利用 ALE 技術將ZnS 應用在薄膜電致發光平板顯示器( Thin Film Electroluminescent (TFEL) Flat Panel Displays )。後來此技術漸漸被導入積體電路的製造,藉由原子層沉積精密控制厚度的特性,可在尺寸更小的元件上進行均勻的鍍膜。傳統的封裝技術(如 CVD、PVD、濺鍍)每一層鍍膜的缺陷密度高,無法形成緻密連續的薄膜(表一),且厚度均勻性與階梯覆蓋率不佳(圖二)。在半導體使用上如以 PVD 或 CVD在溝槽結構上製作電容層,當溝槽深寬比達到7:1時,PVD 與 CD在溝槽開口處沉積電容物質較快,而溝槽底較慢,會導致元件失效。另一方面,在顯示器元件(如 OLED)封裝上也會因部分缺陷而無法形成有效的氣體阻障層,需藉由有機/無機多層膜來避免單一層的缺陷。
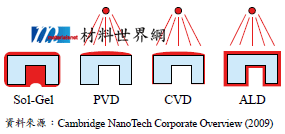
圖二、各種鍍膜技術階梯覆蓋率
原子層沉積具有高緻密性、高厚度均勻性、高階梯覆蓋率、低溫製程與原子級膜厚控制等特點,除了可進行超薄高介電( High-k )材料鍍膜外,亦可針對微小的電路結構提供孔洞填補能力,在具有高深寬比的 DRAM電容結構與微機電元件中提供厚度均勻的鍍膜,在元件封裝上,具有高緻密性的原子層沉積技術漸漸被導入 OLED元件的封裝。另一方面,原子層沉積技術的最大缺點為沉積速度慢,因此各大廠陸續開發出一系列的原子層沉積批次式設備與連續式設備,以改善原子層沉積製程產率的問題。
原子層沉積製程介紹
標準的原子層沉積流程如圖三,可分為四個階段:1.前驅物#1在腔體中進料( Pulse );2.惰性氣體導入,腔體保持真空抽氣狀態( Purge );3.前驅物 #2在腔體中進料;4.惰性氣體導入,腔體保持真空抽氣狀態。在鍍膜過程中,腔體的內部最多只存在一種前驅物,所以不會發生類似CVD的化學反應。所有的接枝反應均在薄膜表面完成,在每一次的前驅物進料中,都提供過飽和濃度反應物給表面的官能基,形成薄薄一層的原子層( 1~2Å ),薄膜表面必須等待第一前驅物反應完成後才可與第二前驅物發生反應,而不會產生類似 PVD的薄膜沉積現象,因此,藉由控制前驅物進料次數,可精準地控制無機層厚度至0.1奈米,而無機物每一層成長的速度約為 0.1~1 sec,厚度約為 1~2Å 之間,每一個鍍膜週期( Repeating Step s)約為5~10秒。
原子層沉積設備主要可分為以下幾項:1.惰性氣體(如氮氣或氬氣)來源;2.前驅物;3.反應腔體與進料管路;4.溫度控制器;5.真空幫浦與廢氣回收裝置;6.微量氣體控制閥。
進料管路與反應腔體是前驅物進行輸送與反應發生的場所,如圖四,前端微量氣體控制閥可精準地控制開關時間至1 ms,藉由真空幫浦的吸力,前驅物與惰性氣體交替的從進料管路輸送至反應腔體,並與基材表面的分子發生反應。前驅物與基材表面反應的速度取決於前驅物的擴散速度與腔體的幾何形狀,適當的前驅物進料量與壓力控制,可在基材表面形成均勻的原子層沉積,但當前驅物劑量不足或壓力控制失常時,則可能會在薄膜表面發生……以上內容為重點摘錄,如欲詳全文請見原文。
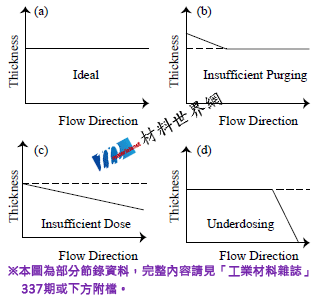
圖五、不適當的壓力與前驅物劑量造成的膜厚不均勻現象
作者:鄞暉恩、龔丹誠/工研院材化所
★完整內容請見下方檔案。