徐煜翔 / 工研院材化所
氮化鋁具有非常優異之物理特性,如高導熱、高電性阻抗、寬能隙與低熱膨脹係數等。這些性質使得氮化鋁可廣泛應用在導熱基板、高功率元件、微電子元件、光電元件、導熱填充料、散熱片、加熱器與承載晶圓的靜電吸盤等。本文將綜覽氮化鋁之國內外產業現況、比較粉體之工業量產方法,並對材料的應用趨勢進行介紹與分析。
【內文精選】
前 言
隨著功能性產品的需求與半導體技術的精進,對於材料有了特定的性質需求,因此也就推動相關材料的開發與應用。氮化鋁為六方晶系之纖維礦型(Wurtzite)結構,由一個鋁原子與四個氮原子以四面體配置的強共價鍵所構成,熔點可達3,000˚C,並具有理論值320 W/m·K之高熱傳導率。其維氏硬度約為12 GPa,破壞強度可達400 MPa以上,且在惰性的高溫環境中非常穩定。
目前氮化鋁在半導體和工業中的相關應用有高功率LED散熱基板、電子電路之導熱基板、散熱封裝材料(Epoxy Molding Compound; EMC)中的導熱填充材、半導體晶圓之靜電吸盤、長晶或磊晶用襯底、壓電材料、高溫坩堝冶具、散熱鰭片、導熱膠材、加熱元件深紫外光之發光二極體、雷射或射頻元件(Radio Frequency; RF)等。
國內外產業現況
國內氮化鋁相關的上中游產品雖然都有廠商持續投入開發中,但面臨的主要問題是氮化鋁材料都從國外進口,在現今各國的自我保護政策下,造成高品質原料取得不易(如德山E Grade氮化鋁粉),價格也偏高,交貨時程拉長,因此難以進行大量研究開發。另外,國內自製之氮化鋁產品品質與國外廠商相比也有差距,因此在性價比上會造成應用推廣的困難。氮化鋁產品的品質受氮化鋁粉料相當大的影響,而粉體的性質又會受原料與合成方法之影響,因此開發新合成方法或是改善現有製程,以提升粉體與產品品質,是一大技術挑戰。
氮化鋁粉體量產方法
目前工業上可量產製備氮化鋁粉體的主要方法有碳熱還原法、直接氮化法與燃燒合成法,而化學氣相合成法雖然可用於製備粉體,但主要還是應用於半導體磊晶或薄膜成長製程中。以不同製程所生產之氮化鋁粉體會具有不同之特性,比如特定雜質含量、粉體外觀或粒度等差異。各製程比較如表二所示。
表二、氮化鋁合成方法比較
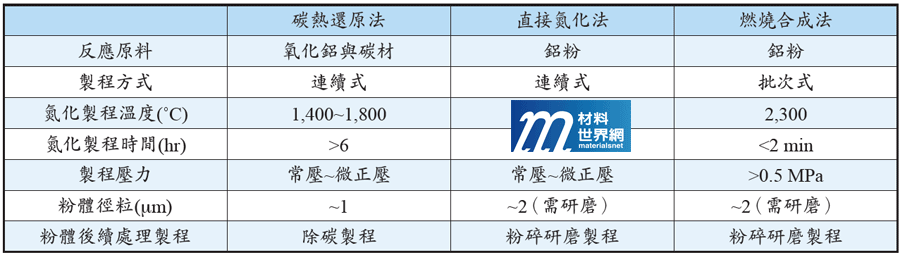
2. 直接氮化法
此方法生產工藝簡單,其優勢在於原料鋁粉取得容易與可連續化生產,只要能控制鋁粉品質,所生產出之氮化鋁品質也能達一定水準之上。然而此方法之缺點為鋁粉氮化反應為高放熱反應,所以氮化過程中的製程溫度高於鋁粉之熔點(約660˚C),因此鋁粉會融熔呈現液態,造成氮氣不易擴散至鋁液或鋁反應錠內部進行氮化反應,故可能會有少量未反應之鋁殘留。氮化反應後的氮化鋁成品會呈現塊材型態,因此需再進行粉碎與研磨等製程,以取得粒度較細之氮化鋁粉體。
3. 燃燒合成法
燃燒合成法不需長時間給予氮化反應所需的高溫環境,其原因為鋁粉氮化為高放熱反應,因此在適當的氮氣壓力下(通常為0.5 MPa以上),當氮化反應一生成時,其放熱量足夠使得週遭鋁粉躍過氮化反應活化能,產生連鎖氮化反應,故只需在反應一開始提供短暫之外加熱源,待氮化反應發生後即可關閉。另外,直接氮化法之製程壓力為常壓,而燃燒合成法則需在高壓下進行反應,因此燃燒合成法為批次反應,造成單一設備產能較低,但其氮化反應時間短暫,大約2分鐘內即可反應完。
氮化鋁市場未來應用趨勢
氮化鋁本身因具有壓電特性,因此可應用在微機電系統上(Microelectromechanical Systems; MEMS),包含陀螺儀、麥克風、指紋傳感器、射頻濾波器、超聲波換能器、自動對焦等元件,且上述也已被廣泛應用於手機系統中,Yole於2020年的MEMS市場報告中也指出,相關元件市場會以年複合率7.4%成長至2025年(圖一)---以上為部分節錄資料,完整內容請見下方附檔。
圖一、2019~2025年MEMS市場成長分析
★本文節錄自《工業材料雜誌》425期,更多資料請見下方附檔。