目前可用於直接製造金屬功能零件的快速成形方法主要有下列幾種:選擇性雷射燒結(Selective Laser Sintering; SLS)技術、直接金屬雷射燒結(Direct Metal Laser Sintering; DMLS)、選擇性雷射燒熔(Selective Laser Melting; SLM)技術、雷射近淨成形(Laser Engineered Net Shaping; LENS)技術和電子束燒熔(Electron Beam Melting; EBM)技術。在眾多針對金屬材料的3D列印製程技術中,選擇性雷射燒熔(SLM)是最具發展潛力的技術。
選擇性雷射燒熔製程控制
SLM製程十分複雜,可調控參數繁多,一般分為四大面向:雷射源相關、掃描方式相關、粉體相關以及基板溫度相關,如圖二所示。在目前主流文獻上,雷射相關參數均著重在雷射功率(Laser Power)的探討,掃描方式相關參數則是著重於掃描速率(Scan Speed)、掃描間距(Scan Spacing or Hatch Spacing)的探討,粉體相關參數則著重於單一粉層厚度的影響,最後基板溫度(Substrate Temperature)亦是影響粉體緻密性的重要因素。緻密性是用來評估SLM製程是否成功最重要也最簡單的方法,尤其相對密度的量測更可有效量化比較。SLM試片的緻密性取決於粉體受熱後所形成的熔池(Melt Pool),是否獲得足夠的熱能以降低其熔液的黏滯性,進而提高流動性與潤濕性,與周圍的粉體形成緊密的接合。因此一般文獻同時也會引入能量密度的公式(見式(1)),來評估在不同製程參數下粉體獲得熱能的差異性。
在SLM製程中,一般公認影響能量密度最大的因素是雷射功率與掃描速率,因此大多會率先建立雷射功率與掃描速率的製程視窗圖(Process Window),確認較合適之參數範圍。圖三是AlSi10Mg粉體於SLM單軌跡製程下,上視及截面之雷射功率與掃描速率製程視窗圖。從圖三(a)可發現,低掃描速率下(700 mm/s以下),外觀呈現扭曲不規則形貌,主要是因為當能量密度(E正比於P/v)增加時,熔池體積增加且黏度下降,使其不規則流動。而降低功率使能量密度下降時,收縮回復壓力的影響會變得十分顯著(固液相收縮率差異),使其呈現扭曲形貌。
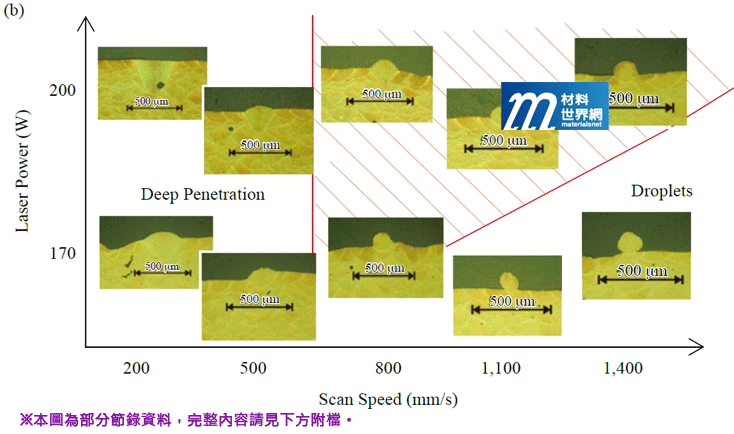
圖三、AlSi10Mg粉體於SLM單軌跡製程下(a)上視;(b)截面之雷射功率與掃描速率製程視窗圖
圖十是使用氣噴與水噴兩種不同製程製備的316不鏽鋼粉體,氣噴的粉體形貌多呈圓形,如圖十(a)所示,平均粒徑約20μm。水噴的粉體形貌如圖十(b)所示,呈現較不規則,平均粒徑約30 μm。圖十一是將圖十中兩種不同粉體在不同粉層厚度下,進行SLM成形後的試片孔洞觀察。圖十一(a)是氣噴粉體在粉層厚度0.05 mm的參數下製備SLM試片,可發現結構十分緻密,只有零星分布的微孔。然而在相同氣噴粉體但粉層厚度較厚的SLM試片上,可看到許多規律分布的孔洞以及較差的粉體結合現象,如圖十一(b)。而粉層厚度0.1 mm用水噴粉體製備的SLM試片,可觀察到相較氣噴粉體有更多的孔洞(圖十一(c))。從EDX資料中可發現水噴粉體相較氣噴粉體而言有較高的氧含量,氧化物是降低潤濕性的主因…以上為部分節錄資料,完整內容請見下方附檔。
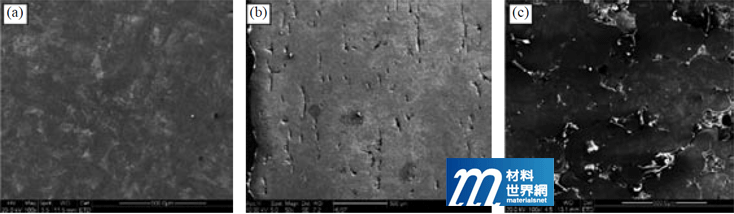
圖十一、氣噴粉體於粉層厚度(a)0.05 mm;(b)0.1 mm以及(c)水噴粉體於粉層厚度0.1 mm下製備SLM試片之微結構SEM照片
作者:蔡恆毅 / 工研院材化所
★本文節錄自「工業材料雜誌」369期,更多資料請見下方附檔。