玻璃纖維複合材料
自 1932年 Owens-Illinois 公司 Games Slayer 研究員發明玻璃纖維的製造法後,第一台以玻璃纖維為車體的概念車 Stout Scarab 於 1946年在美國底特律誕生,但當時並未大量生產。直到 1953年,Robert Morrison 以 Molded Fiber Glass(MFG) 製程為Chevrolet提供玻璃纖維複合材料,以生產史上第一台全 FRP車身汽車 Corvette,這輛配備150匹馬力的雙座跑車,當時售價 3,500美金,僅提供 VIP級客戶,預計生產 10,000台,但總共生產 3,600台後即停產。
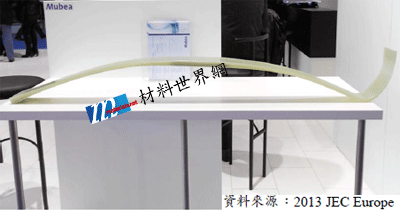
圖一、玻纖複材葉片彈簧
碳纖複合材料
近年來碳纖維價格逐漸下滑,其製品也逐漸平民化。2011年發表的 BMW M3 CRT(Carbon Racing Technology)使用碳纖複材前座椅、發動機罩,將重量/功率比降到 3.5 kg/hp。2013年BMW宣布量產城市通勤電動車 i3,採用全碳纖座艙,如圖三、圖四、圖五,儘量減輕車體重量以容納更多的電池來增加行駛距離。同時,輕量化也意味著撞擊時的衝量減少,吸能結構的需求也降低,又可進一步減輕重量。
碳纖複材質量輕而剛性高,故除了車體結構等固定件外,若能應用於運動件,則對於能量損耗的降低,更有幫助。第一個小客車用的全碳纖複材輪圈原型在 2008 年出現於日本Weds Sport賽車,隨後澳洲 Carbon Revolution開始供應 CR-9規格的碳纖複材輪圈,一組售價約 15,000美金。
平價碳纖與自動化製程帶動汽車產業成長
根據Toray的市場預估,由現今到2020年,全球碳纖複材產業於運動器材部分成長趨緩,航太產業維持成長,而包括汽車等工業產品的市場將急速成長。然此成長也非一蹴可幾,初期限於製作成本,僅有金字塔頂端的豪華車種開始採用傳統熱固型(Thermosetting)的碳纖複材,隨著碳纖維本身價格降低,與RTM等製程的改進,以及熱塑性(Thermoplastic)複材與自動化製程的導入,才會逐漸滲透普及到比較平價的車種。
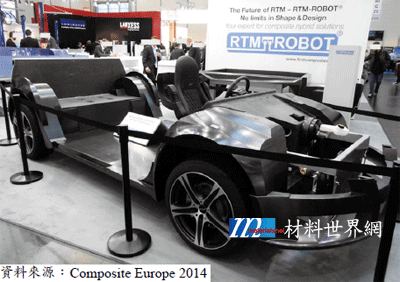
圖八、RTM成型電動車底盤
目前碳纖複材之基材樹脂仍以熱固型樹脂為主,然而傳統熱固型纖維複材成型時間長,模具使用效率低,成為量產瓶頸。為縮短製程時間,提高模具使用效率,熱塑性纖維複材逐漸受到重視。根據碳纖維大廠Toray公司於2012年的預測,碳纖複材應用於汽車產業,將於2015年急速成長。初期仍以熱固型碳纖複材為主,因受限於成本與量產性,僅有超跑及豪華型車款會使用,每年全球產量僅約5百萬台,主要部件包括傳動軸、引擎蓋與行李廂內部支撐結構、座艙底盤等。
自主熱塑纖維複材技術
常見之熱塑性纖維複材之基材樹脂包括聚碳酸脂( Polycarbonate; PC )、丙烯腈丁二烯苯乙烯( Acrylonitrile Butadiene Styrene;ABS )、聚醯胺( Polyamide;PA )如尼龍等。其與熱固型基材樹脂最大之不同在於遇熱可重新塑型加工。此外,碳纖維在出廠前會於表面塗佈一層極薄的上漿劑( Sizing )以保護纖維不致摩擦斷裂,目前市售碳纖維表面之上漿劑絕大多數依熱固型樹脂之潤濕性( Wetting )而設計,其與熱塑性樹脂的潤濕性不佳。
工研院材料與化工研究所因應此一未來需求,自 2013年起即發展水相環保型之纖維微乳液技術,利用改質微乳化漿液改善纖維與塑料表面親合,以微胞合成技術促進纖維與基材間表面親合力,控制基材與纖維之含浸。選用同時與基材及纖維鍵結性較佳之單體,並設計水相環保型之纖維微乳液,其微胞尺寸約為 300奈米,易含浸於纖維,可確保界面強度符合需求,使熱塑性纖維複材產品特性得以提升 ……以上為部分節錄資料,完整內容請見下方附檔。
作者:邱佑宗 / 工研院材化所
★本文節錄自「工業材料雜誌340期」,更多資料請見下方附檔。