電子元件構裝過程中,由於晶片、模封樹脂、基板等各組成材料的熱膨脹係數與彈性模數的差異,以及樹脂反應所造成的體積收縮,導致構裝過程或構裝後的翹曲,甚至影響後續的加工。因為作為構裝主體的晶片熱膨脹係數極低,僅約 2.8×10-6/˚C,為降低翹曲,各材料供應商無不竭盡所能,降低其產品之熱膨脹係數,以與晶片的材料性質匹配。
然而, 參與構裝的材料種類繁多,其熱膨脹係數受限於本質,極限值不盡相同。要降低熱翹曲,並非一味追求個別材料的熱膨脹係數,而須考量其間的匹配。有限元可以模擬構裝過程或最終的翹曲,評估材料的適用性,故廣為業界採用,作為篩選材料的先期評估。另一方面, 可以從材料設計的角度來看這個問題。對於有能力調整材料性質的材料供應者,可以針對目標客戶,配合其慣用的其他材料,設計客製化的構裝材料,以達到低翹曲的目的。優化( Optimization )演算或稱最佳化,即可協助材料供應者達到目標化的材料設計。本文即簡單介紹此一主題。
構裝案例材料及製程簡介
本文藉由一構裝案例說明模擬與優化的流程。構裝使用的基板如圖一,晶片以錫球連接於載板後如圖二,模封完成後如圖三。在計算模型方面,單一晶片幾何尺寸如圖四,晶片長寬為 8 mm,厚約 200μm;載板區域長寬為 12 mm;封裝單穴幾何則如圖五,載板區域為 42 mm × 42 mm;模封區域為 38 mm × 38 mm(虛線範圍),其中有 9片晶片如 3×3 排列,間隙 0.1 mm。單一晶片底部 I/O 數為 1502,如圖六,約為 39 mm × 39 mm。載板連同晶片沿厚度方向之尺寸如圖七,載板厚度約 100~400 μm不等。因接腳數過多,故模擬時採用等面積的方形區域代替錫球。模擬採用之晶片、錫球、底膠等材料參數如表一。
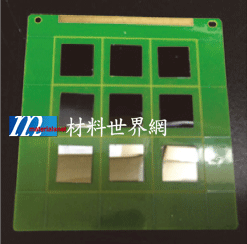
圖二、晶片以錫球連接於基板
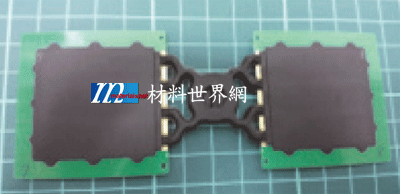
圖三、模封完成
模擬封裝歷程之晶片如圖八:1.首先在初始狀態 270˚C,黏上錫球;2.降溫至 170˚C,充填底膠(Underfill);3.降溫至 150˚C,充填模封樹脂(Overmold);4.降溫至 25˚C,冷卻;5.將單一晶片自 3×3 模封切出。
以優化模擬進行材料設計
計算模擬的目的除了與實驗互為印證外,也希望能藉此提供封裝尺寸與材料性質參數之間的最佳匹配,以降低最終封裝後的翹曲量。例如,對於一封裝材料的供應者,有能力根據客戶的需求調整材料的性質,包括熱膨脹係數、彈性模數等;但是有許多材料,其性質又互相影響,要如何匹配才能達到最低翹曲的目的?當然以地毯式搜索的方式來進行大規模的計算,可作詳盡的探討,但其所耗費的時間龐大,不符合效益。基於以上所述,使用者可利用優化演算方法,以尋求低翹曲量的最佳材料性質組合。圖十為優化技術之系統概念模型,所謂“優化”,係指調整一組參數,符合所有限制條件( Constraint ),且所需的代價最小,例如應力、體積、重量等。優化須考慮的項目包括:
2.狀態變數(State Variable; SV):
為因變數(Dependent Variable),為了實現優化的邊界條件,故必須是設計變數的函數。狀態變數量可能會有上下限,或僅有單方向的限制,即只有上限或下限。然在本文案例中,無狀態變數……以上內容為重點摘錄,如欲詳全文請見原文。
作者:邱佑宗、陳凱琪、李巡天/工研院材化所
本文節錄自「工業材料雜誌333期」,更多資料請見:https://www.materialsnet.com.tw/DocView.aspx?id=17093