隨著綠色能源議題持續受到關注,功率模組在太陽能、電動車與油電混合車等領域的應用市場也逐漸擴大。目前功率模組往高功率、薄型化以及高密度化進行整合與開發。導熱封裝材料隨著功率模組的演進需求,除了追求高導熱係數之外,也開始出現不同的應用規格與變化。在電動車與馬達應用中,如何提高嚴苛環境下的可靠度,包含耐熱性以及耐腐蝕性,將會是未來車載功率模組應用的重要議題。
本文將從以下大綱,針對最新的功率模組市場趨勢及發展進行說明,並介紹功率模組用封裝材料未來研發方向。
‧功率模組產業趨勢與市場現況
‧功率模組用封裝材料市場與應用
‧功率模組用熱介面材料市場與應用
‧熱介面材料在功率模組中的重要性
‧功率模組薄型化產生的材料與結構變革
‧功率模組用導熱封裝材料研發方向
‧工研院材化所薄型化導熱材料開發現況
【內文精選】
功率模組中與散熱直接相關的封裝材料共有兩大項,分別是整顆模組的封裝外殼(Molding Material),以及直接傳遞晶片熱點的熱介面材料1 (TIM1)與將底板熱傳遞至散熱鰭片的熱介面材料2 (TIM2),如圖一所標示。
功率模組產業趨勢與市場現況
在未來,功率模組將會有三大重要市場,分別為家用變頻系統、電動車以及工業控制應用。隨著功率模組的功率密度越來越高,新一代寬能隙(Wide Band Gap; WBG) IGBT功率模組將會是未來發展的趨勢,其晶片將從Si轉變至SiC以及GaN。以材料本質來說,SiC相較於Si有兩倍的電子飽和速度、三倍多的熱傳導率以及十倍的絕緣破壞強度,因此製備成元件後,其低導通電阻將可以減少元件的功耗,並且可以在200˚C穩定運作,速度將會是Si模組的數倍。
功率模組用熱介面材料市場與應用
熱介面材料(TIM)包含散熱片、相變片、散熱膏、間隙填充物、散熱黏合劑等。2016年全球市場規模為6.4億美元,隨著汽車領域市場的需求增加,2017年將成長8.6%,達6.9億美元,預估2020年增加至10.5億美元,每年有近乎10%的成長。TIM是現今最普遍使用的熱管理材料,有別於散熱結構(例如散熱鰭片、Heat Sink)是將熱源傳遞過來的熱,藉由熱對流或熱輻射的形式發散至外界,使得元件得以降溫,TIM主要的功用是填補兩種材料接合時所產生的微空隙及物體表面的孔洞,減少熱傳遞的接觸熱阻,如圖六所示。空氣孔洞的導熱係數只有0.026 W/m·K,等於是絕熱的介質,因此選用合適的熱介面材料維持熱傳導路徑在功率模組中是相當重要的。
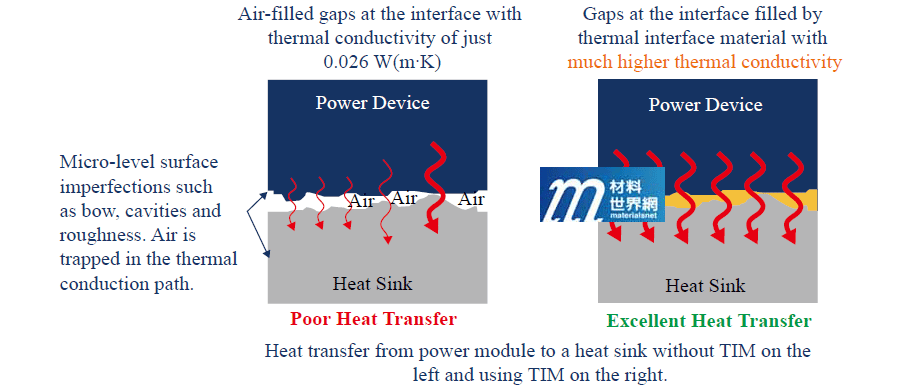
圖六、TIM於功率模組之功效
常用於功率模組的膜與片型態TIM如表二所示。其材料選擇多樣性,也有複合式膜層的設計,如絕緣特性非主要要求,也有添加金屬粉體達到導熱係數86 W/m·K的選擇。
表二、膜與片型態之TIM
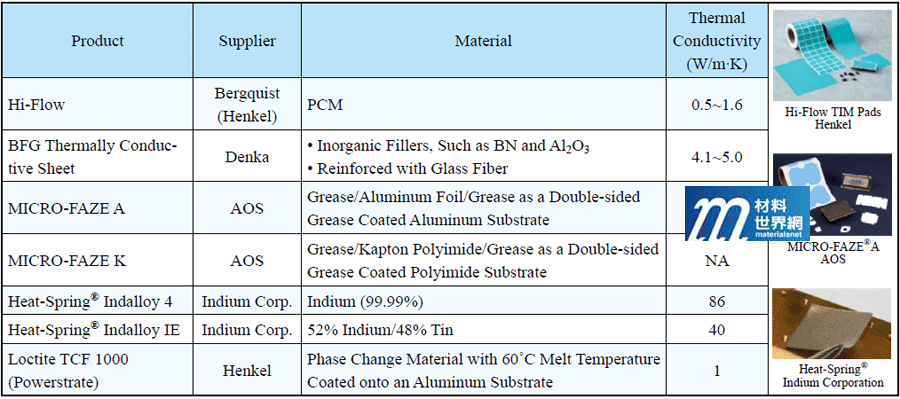
功率模組薄型化產生的材料與結構變革
在功率模組的結構中,DBC陶瓷基板扮演了乘載IGBT以及各式被動元件的功能,陶瓷基板上可直接佈線路,並且具有極佳的熱傳導特性。然而,由於陶瓷基板的製程必須加熱到千度以上以將銅片與陶瓷進行燒結,因此DBC基板的成本也相對較高。隨著功率模組薄型化的發展,基板與底板的一體化、製程簡化以及成本降低,便成為一個新的趨勢。近年來,德國與日本已成功發表了IMS (Insulating Metal Substrate)與IMB (Insulating Metal Baseplate)技術,如圖十所示。這兩項技術皆是透過一層導熱接著材料(如TIM),將下層銅箔與上層銅板進行壓合製程。此導熱接著材料厚度為100~200 μm,具備低溫加熱可接著的特性。目前技術領先國為日本,其導熱係數為8 W/m·K,破壞電壓在100 μm下為2.5 kV…...以上為部分節錄資料,完整內容請見下方附檔。
作者:劉彥群/工研院材化所
★本文節錄自「工業材料雜誌」380期,更多資料請見下方附檔。