近年來電子及光電產品多朝向輕薄、可撓及大尺寸螢幕發展。玻璃透過金屬化程序,建構出精密金屬網格電極替代ITO,能大幅改善傳輸時造成的電能耗損,並同時提供高透光度。玻璃金屬化後亦可被使用作為半導體封裝的中介層材料。目前半導體產業正在經歷重大轉變,三維整合及堆疊封裝是轉型的重要關鍵。中介層可改變晶片在系統中組裝和互連的方式,藉著中介層互相連結,增加單位面積內的元件密度,使得產品微型化時可減少功率損耗、降低成本、提升元件性能。由於尺寸和成本方面的因素,矽導通孔的三維堆疊在存儲器與感測器中的使用受到限制。玻璃中介層因製造成本低且無尺寸限制之優點,使其成為非常合適的替代選擇,而玻璃與金屬之間的附著力好壞則為中介層製程之重點。
玻璃上金屬線路的應用
由於玻璃與矽的熱膨脹係數(Coefficient of Thermal Expansion; CTE)匹配,且機械強度高、表面光滑、製造成本低、有惰性及抗濕性、可進行高密度輸出/輸入的封裝設計,使得玻璃搭配金屬被廣泛使用作為光電元件材料或是微機電(MEMS)系統與感測器之封裝材料。
表一列出了玻璃、金屬和陶瓷相比的性能,透過比較,可以看出玻璃作為封裝材料的理想性質。在連續的面板級裝配過程中,為了使微機電系統和感測器生產率更高,會根據面板尺寸與成本考量,以超薄玻璃為基礎,使用有蓋與空腔封裝增加產量,該封裝技術適用於生物感測器、電化學感測器、壓力感測器、影像感測器和汽車視覺系統的雷達模組。將此理想的封裝材料與金屬結合,更是在半導體封裝產業中被當作是最具潛力的中介層(Interposer)材料之一。
玻璃金屬化技術
於非導體材料如玻璃或陶瓷上進行金屬化,傳統是選用物理氣相沉積(Physical Vapor Deposition; PVD)方法,如真空蒸鍍(Vacuum Evaporation)或濺鍍(Sputtering)。在日常生活中所使用的鏡子,就是使用蒸鍍製程,在低壓狀態下藉由高溫將鋁蒸發成氣體,鍍在玻璃背面上,然後再塗上一層阻絕水氣且固定金屬的保護漆。而濺鍍法的原理是在高真空狀態時施加電壓會產生電場,在此電場的作用下通入氬氣,氬離子會形成高能的Ar+離子衝擊靶材,使靶材原子形成超微粒子濺出並沉積在材料表面上(圖一)。幾乎任何材料均可使用濺鍍法,能形成無汙染附著性良好之鍍層,鍍層應力也較低,在低厚度狀態下附著良好。但濺鍍的靶材利用率只有三到四成,導致濺鍍法的成本很高,無法負荷高厚度的要求。
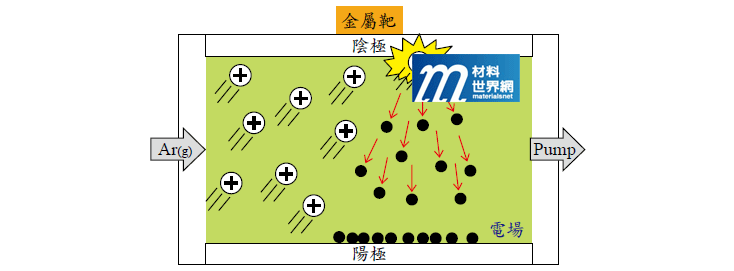
圖一、濺鍍示意圖
基材上提升附著力的方法
近十餘年來,運用自組裝膜來固定活性點進而增加鍍膜附著力的研究也不斷出現。主要是使用有機矽烷類(Alkylsilane)與有機硫化物類在晶圓或玻璃表面形成自組裝單層膜(Self-assembled Monolayers; SAMs),而賦予基材表面特定之功能,因有機矽烷其頭端基團如氯或烷氧基(文獻中常見甲氧基或乙氧基)會水解轉變為活性基團如羥基(-OH)與基材反應,形成穩定的化學鍵結。而末端基團如胺基(-NH2),巰基(-SH)或異氰酸(-NCO)則決定了所形成自組裝單層膜的化學性質,如親水性或疏水性、極性或非極性等(圖四),透過末端基團所帶的電性吸引或是經由形成配位鍵,將活性點固定於自組裝單層膜上,金屬膜便會在活性點上形成。而所製造出的金屬附著性經常優於微蝕刻所能產生之效果。
工研院材化所精密蝕刻及表面技術研究室利用上述有機矽烷自組裝膜濕式製程取代傳統的PVD,使用不同官能基的矽烷形成自組裝薄膜,作為催化劑與基材之間的橋梁,連接催化劑進行無電電鍍金屬沉積,流程如圖五所示。成功的利用此技術在高深寬比(開孔約5 μm,深度約60 μm,AR≒12)矽盲孔(Through Silicon Via; TSV)的晶圓基材上,沉積一層均勻分布的金屬層,後續再利用電鍍增厚填滿,由圖七中可以見到孔洞中形成連續完整的鍍銅層。將同樣的有機矽烷自組裝膜濕式製程加以變化,本實驗室也成功在玻璃之上沉積出高附著力之銅層,沉積厚度可達10 μm以上,且經過標準之百格測試,附著力可通過4B之規範…...以上為部分節錄資料,完整內容請見下方附檔。

圖五、不同步驟後基材表面狀態示意圖
作者:顏銘翬、林子婷 / 工研院材化所
★本文節錄自「工業材料雜誌」370期,更多資料請見下方附檔。