材網編輯室/工研院材化所
植物由來的新材料「纖維素奈米纖維(Cellulose Nanofiber;CNF)」,其相關利用正不斷地創新擴大,在實務上被廣為運用,而重要性日益顯著。隨著複合材料(CNF強化樹脂)製程技術的進展、製造成本的降低,在汽車領域的實用化也逐漸展露曙光。除了強化樹脂之外,利用CNF變化多樣的優異特性,日本各領域企業紛紛投入CNF製品研發的行列。
CNF擁有多項優異性能,故被喻為「夢想中的新材料」。主要特性包括①輕量且具有高強度,纖維重量僅為鋼的5分之1,但擁有5倍以上的強度;②熱變形量小;③表面積大;④透明度高;⑤具阻氣性;⑥可賦予液體獨特之搖變性(Thixotropy)等。
此外,CNF來自於植物,因此對環境的負荷小,具永續發展性。日本森林資源豐富,在CNF的技術研發及製品開發方面均領先全球,相對於世界各國,日本擁有材料上的優勢地位。日本經濟產業省除了提出在2030年日本國內CNF相關材料市場要達到1兆日圓之目標外,同時也計畫推動成立世界首項CNF國際標準。
產業界中對於CNF投以熱切注目眼光的還包括了汽車產業。由於CNF會在樹脂中形成纖維網狀結合的構造,因此可製造出輕量且具高強度的CNF強化樹脂。若以CNF強化樹脂取代混合了滑石(Talc)或玻璃纖維等強化材料之聚丙烯(PP)成形的一般樹脂製汽車零組件,經試算約可減輕25%的重量,一輛汽車約可達到減輕20公斤重量之輕量化效果。
曾與豐田汽車(TOYOTA) 合作進行碳纖維強化塑膠(Carbonfiber Reinforced Plastics;CFRP)製車體之實用化研發的金澤工業大學教授影山裕史表示,同樣是輕量化材料而可望受到廣泛採用的CFRP,因強度較CNF強化樹脂更高,適用於車體的骨架組件;而CNF強化樹脂則朝向排氣罩(Hood)或車門等外板、內裝用組件持續發展,未來可預見不同材料將會「適材適所地朝向實用化發展」。
「京都製程」與「TEMPO氧化CNF」
過去一直無法跳離基礎研究領域的CNF,近來對於實用化的期待急遽提高,主要是因為2016年時京都大學的矢野浩之教授開發了一項革新的CNF強化樹脂生產技術「京都製程(Kyoto Process)」。一般的強化樹脂生產製程必須投入1公斤價格約數千~1萬日圓的強化材料CNF,然而「京都製程」無須事先製作成CNF,僅須投入經過化學處理的紙漿即可。據矢野浩之教授表示,以此方法製造的CNF成本「1公斤將可落在500~800日圓」。
「京都製程」首先是將紙漿進行化學處理後成為變性紙漿,接著投入射出成型機,在混練、射出成型過程中,可以同時進行從紙漿中抽出CNF奈米化(奈米解纖),以及在樹脂中分散CNF(樹脂複合化)兩項處理作業。一般的強化樹脂生產製程則是紙漿經過機械處理之後得到CNF,再經脫水、化學處理製作出變性CNF,投入射出成型機分散CNF之後,製作出CNF強化樹脂。京都製程將2項工程匯集成1項,因此大幅削減了成本(圖一)。此外,一般製程須將含水份的CNF先經過脫水程序再進行化學處理,而京都製程則無須進行任何水處理相關作業,省略水處理流程有助於製造成本的削減---以上為部分節錄資料,完整內容請見下方附檔。
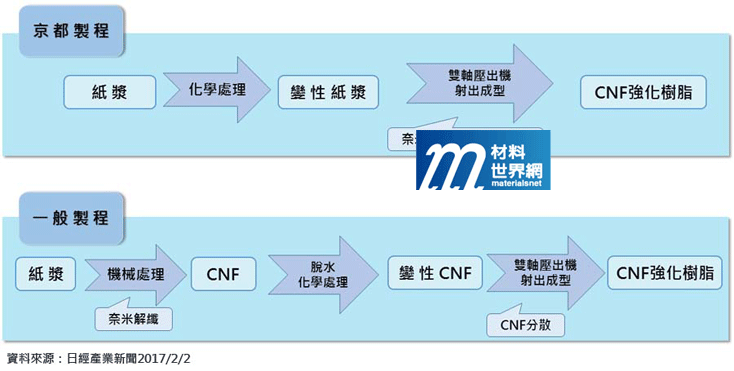
圖一、CNF京都製程與一般製程