微米針陣列
隨著科技快速發展,對於醫療技術的審視不再僅止於療效,也開始逐漸著重於對人文的關懷,如何提供患者一個更為愉悅的診療環境已成為醫療發展的當務之急。傳統上,藥物施放多採皮下注射或口服的治療方式,雖能有效地輸送藥物,但卻容易引起感染和疼痛,不但較為耗時,亦造成病人在臨床治療上的痛苦。因此,近年來經皮給藥系統(Trandermal Drug Delivery System)的診療方式開始快速發展,微米針(Microneedle; MN)陣列(Microneedle Array)即為此概念下應運而生的新型生醫注射技術,此方法能降低病人的組織破壞,減輕病人在治療上的疼痛,達成促進重點照顧檢驗(Point-of-Care)的醫療手法,提供即時性的病情監控與照料。
微米針陣列是利用微機電製程技術將針頭微小化,由數十微米的針頭以矩陣排列方式組成,此微小針頭不但能穿透皮膚的角質層,亦不會刺激深層組織的痛覺神經,使病人在臨床接受藥物注射時大幅地降低疼痛感,實現了無痛注射的目的。
微米針可依其微加工模式分為In-plane型態及Out-plane型態,也可依其構造分為實心微針、中空微針及半中空微針。中空微針適合於更精準的藥物劑量控制,可以配合藥物釋放控制進行長期給藥,也可以結合加壓注射將藥物快速送出;而實心微針主要經由擴散讓塗抹於針頭的藥物傳送。藉由不同的製程技術,各種功能性的微米針陣列被發展出來,廣泛用於藥物注射、血液萃取、癌症診斷與微透析等醫療技術,目前常採用微米針陣列的材料與結構整理如表一所示。
應用於微米針陣列的微機電製程
微機電系統係指在一般矽晶圓上透過微製造技術(Micro-fabrication)來製作與整合機械元件、感測器、致動器與電子元件等的微加工方法。運用MEMS技術可以製造出較大面積的微米針陣列。常用的製程方法有改良過的LIGA微製造技術,或是反應式離子蝕刻(RIE)和等向性蝕刻技術的組合,或是飛秒雷射雙光子聚合、X-ray深光刻術製程(DXRL)、黃光微影(Photo Lithography)製程、感應耦合電漿(ICP)蝕刻、聚焦離子束(FIB)輔助技術等。
文獻中最常見的微針陣列是在矽晶圓上製作而得的矽針陣列。首先採用紫外光(UV Light)曝光的方式進行微影(圖二(a)),在表面有一層二氧化矽的矽基板上塗佈光阻,定義出微針陣列的位置與直徑(圖二(b))。先蝕刻二氧化矽層,使其形成Mask,去除殘餘光阻後(圖二(c)),接著可搭配濕式或乾式蝕刻製程,經由Underetching的效應,最後會形成微針的結構(圖二(d)),一般而言,濕式蝕刻成本低、較易操作,然而在微針的高度及微針間的距離控制上較受限制,乾式蝕刻則大致相反。針狀的微針陣列便是透過氫氧化鉀(KOH)對矽進行非等向性蝕刻所形成。
圖二、針狀頂端的微針陣列之製程流程
再者矽微米針陣列製作的成本也令人踟躕不前,這些陣列通常都是透過昂貴又費時的半導體製程製作,且須在無塵室的環境下作業,更何況利用微針骨架上翻製中空微針時,微針骨架通常只能使用一次,因為微針骨架會黏附在最終產品上或是在過程中就成為犧牲品。這種消耗性的骨架大幅增加最終產品的成本,不容易滿足大量生產及低成本的要求。因此近年來逐漸發展出一種製作策略,在矽基板上製造大面積的矽針後,並非直接使用,而是將其做為模板,以熱印壓模技術和精密電鑄技術翻鑄一個微針陣列的母模,接著再運用母模將其他材料如高分子或金屬填入,大量生產高品質的微針陣列。如此一來就能解決大量生產及低成本的問題,而製造出的金屬或高分子聚合物微針陣列也比易碎之矽針更加強韌和耐用。翻鑄微針陣列的製造程序主要包括三個過程:②接著使用PDMS母模,再以熱印壓模技術翻製出一個PMMA實心微針陣列,如圖四(b)所示;③在PMMA實心微針陣列表面以濺鍍或無電鍍技術形成一層奈米金屬薄膜做為導電層,以利於接下來運用電沉積技術翻製出金屬中空微針陣列,如圖四(c)所示。
接下來此高深寬比微針陣列進一步透過微加工方式來形成中空狀的錐狀結構,以達到藥物注射、血液萃取等目的。所採用的製程流程如圖六所示,首先利用濺鍍方式先後沉積10奈米的鉻層與100奈米的銅層做為電鍍的晶種層,接著採用電鍍製程來沉積均勻的鎳層於微針結構的表面。為了製造微針的缺口,再次旋塗上SU-8光阻於微針表面後進行機械拋光,直至微針的開口裸露出來;去除沉積在微針表面的光阻後,再透過乾蝕刻方式將金屬鎳所構成的微針內部之光阻去除,即可形成中空狀的微針結構……以上內容為重點摘錄,如欲詳全文請見原文
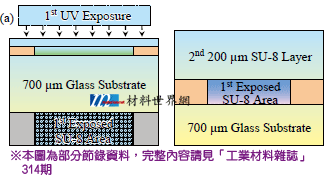
圖五、錐狀的微針陣列之製作流程
作者:陳嘉勻、顏佳瑩、李文錦 / 工研院材化所