有機發光二極體(OLED ,或稱有機電激發光)技術一直被認為是最具競爭力的下世代發光及顯示技術之一。其具有自發光的特性、不需背光模組、極薄(<10µm)的元件膜層,被認為是可以大幅減低材料成本的絕佳優勢。低操作電壓及高發光效率也被認為是新世代超薄軟性顯示器及平面式節能固態照明的實惠選擇。
目前OLED 量產的主流是真空蒸鍍方式,將有機材料在高度真空的條件下,以加熱昇華的方式,氣化並均勻沉積在需要的基板上。這樣的蒸鍍方式需要真空製程及蒸鍍遮罩等較昂貴的固定成本,且在製程中有極低的材料使用率。根據美國杜邦公司的評估,目前蒸鍍OLED 的成本仍高於同尺寸的LCD (圖一),也就是OLED 並未發揮其原來被認為結構簡單、材料需求少的優勢。
何謂低成本製程技術?
成本考量大約可分成固定成本與操作成本兩大類。固定成本主要來自廠房建設、設備投資、管線等硬體與土木建築。而操作成本包含水、電、人工、氣體及生產原料(包含有機材料、靶材、金屬、基板與封裝膠材等)。在能源消耗部分,通常都只著重於產品出廠後的能源效率,但幾乎忘記了產品生產時的能源消耗。圖二是Add-Vision 公司針對高效率蒸鍍小分子與低效率塗佈高分子兩個極端的案例做評估,發現兩種元件的生產能源消耗分別是~1,000 MJ/m2 與~100MJ/m2 。若換算成每平方公分的單位,分別是100 KJ/cm2 及10 KJ/cm2 。
小分子OLED 的塗佈技術
2. 噴墨、噴灑、狹縫式、噴嘴塗佈
連續出液方式包括狹縫式及噴嘴式,只是前者是線源(Linear Source),後者是點源(Point Source)。表一為Panasonic 電工評估常見可大型化塗佈方式比較。根據該公司評論,雖然成膜的均一性皆有一定水準,不過噴墨式的製程在大型化的困難度較高,且由於出液為非連續式液滴形式,容易造成局部不均勻的現象。另外,非連續式的噴霧式也有材料使用率較低的問題發生,所以目前Panasonic 在開發溶液製程OLED 時,主要採取狹縫式塗佈的製程。
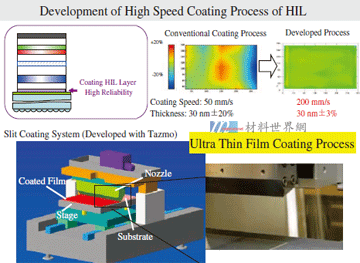
圖六、Panasonic電工與TAZMO在NEDO計劃下合作開發的狹縫式塗佈製程成果
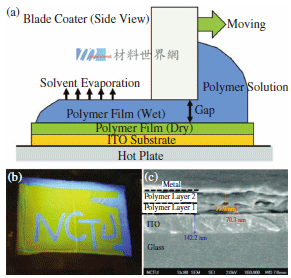
圖十四、刮刀式塗佈高分子製作PLED 元件
多層膜堆疊技術
多層膜的堆疊在傳統真空蒸鍍式的製程中是沒有問題的,依據時間差而堆疊的膜層,由於是固體,也沒有溶劑,各層間在製作的過程中沒有互相混溶的情形。然而,濕式塗佈製程由於多少需要溶劑,上層正在塗佈的溶劑非常有機會在塗佈的過程中,移動到下面已經乾燥的膜層,造成下層材料的再溶解,使得應該分層的材料混合了。以下是幾種可能的解決方案。
2. 溶劑控制與移除
目前的塗佈技術大致可分為自身計量式(Self-metering)及預先計量式(Pre-metering)等兩類。自身計量式的塗佈特性是指塗膜厚度受限於流體物性、塗佈機台幾何參數與操作條件控制,而此類的塗佈方式包含浸沾式塗佈(Dip Coating)、滾筒式塗佈(Roll Coating)及刮刀式塗佈(Blade Coating)等。相對於前者的塗佈方式,預先計量式的塗佈特性是塗佈膜厚可依產品的需求,預先由幫浦流量及塗佈速度做事先估算的塗佈方式,常見的有狹縫式塗佈(Slot Coating)、淋幕式塗佈(Curtain Coating)及斜板式塗佈(Slide Coating)等。
工研院目前進展
工研院在過去數年累積了許多小分子高效率磷光發光材料技術,在轉進溶液製程後,先後發表了高效率且溶液/ 蒸鍍製程通用之黃光(PO-01-TB ,圖十七(6))與綠光(CF3BNO-acac ,圖十七(5))材料,以及溶液/ 蒸鍍製程通用、藍光適用之高效率主體材料(CzDBS),搭配驗證型旋轉塗佈製程,成功開發出溶液製程白光 (18.4 lm/w @1,000nits)與綠光元件(17.3 lm/W @1,000 nits)。其他如藍光、紅光與熱聚型材料的開發也正在進行中。在製程部分,工研院也正積極地調整目前學術驗證型的旋轉塗佈製程,轉進到與世界技術接軌的狹縫式塗佈,並進行其他新穎塗佈技術導入的評估工作。相信不久的將來,工研院藉由材料與製程兩方面的配合,可加速開發並與領先公司並駕齊驅……以上內容為重點摘錄,如欲詳全文請見原文
作者:廖鎔榆 / 工研院材化所
★本文節錄自「工業材料雜誌305期」,更多資料請見:https://www.materialsnet.com.tw/DocView.aspx?id=10308